FABRICATION
Alcotuff is versatile formability, it can be bent, cut, and formed according to your architectural need.
01 CUTTING
Alcotuff can be cut using a wide variety of machines and tools such as table saws, hand circular saws, panel saws, shear cutting. A suitable saw blade is a carbide-tipped blade for aluminum or plastic use.
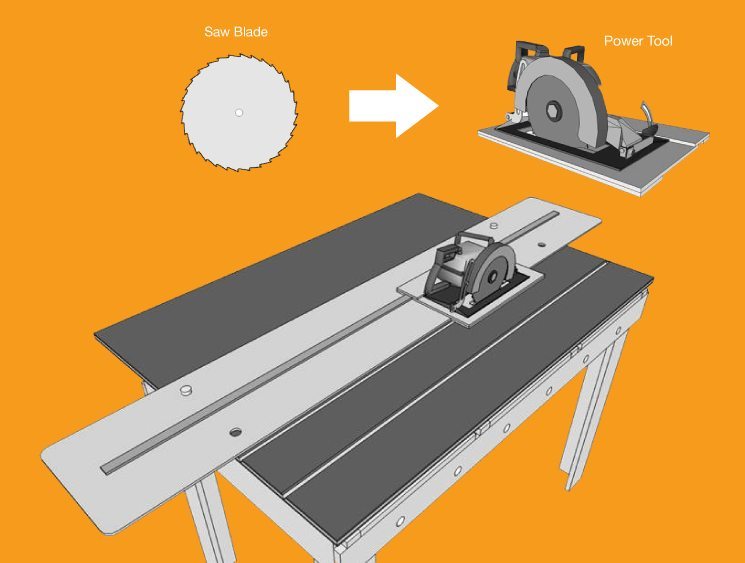
02 ROUTING & GROOVING
Routing, grooving, and folding are usually needed to form a variety shapes or sizes. In this process, the back surface of Alcotuff is cut forming a V-shaped or rectangular one, using disc or end milling cutter. The front surface of the aluminum cover and part of the core are retained to enable it to be folded. Please ensure to leave at least 0.4mm thickness of the core.(see pict 3.2.1 and pict 3.2.2)
The recommended minimum distance of the grove line from the panel edge is 20mm
( see pict 3.1)
Using the computerized CNC machine to do the routing or grooving process is recommended to ensure the accuracy, and efficiency.
Alcotuff folding process is shown in pict 3.3 – 3.6
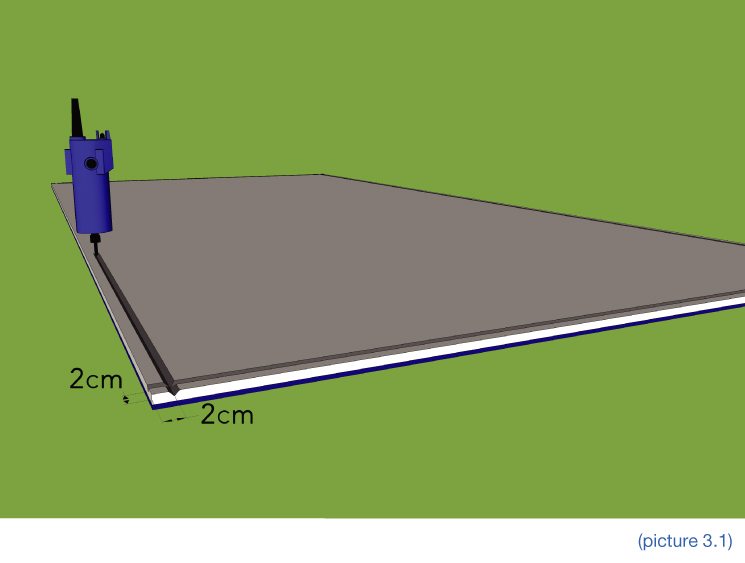
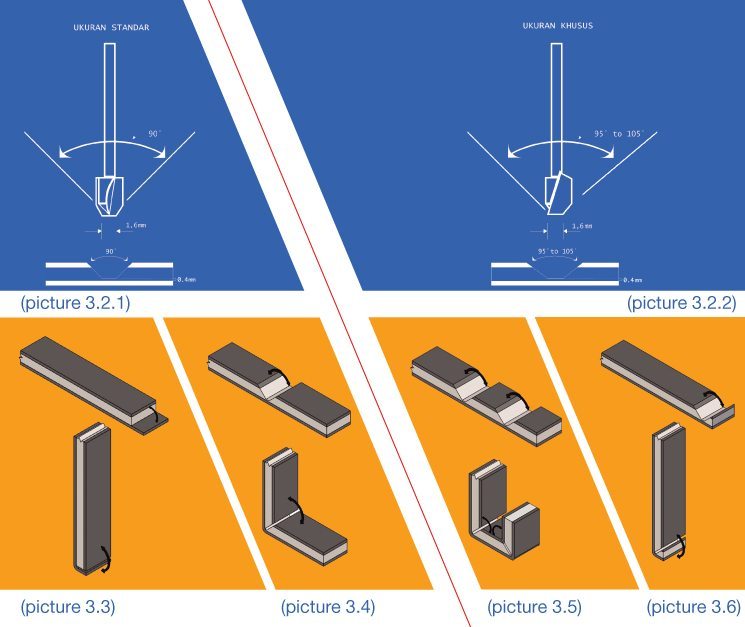
03 BENDING
A. Bending process using pyramid roller machine will allow various bending radius (see pict 4.1)
B. Using clamped pipe machine (see pict 4.2). Note: max bending radius is 30 degree.
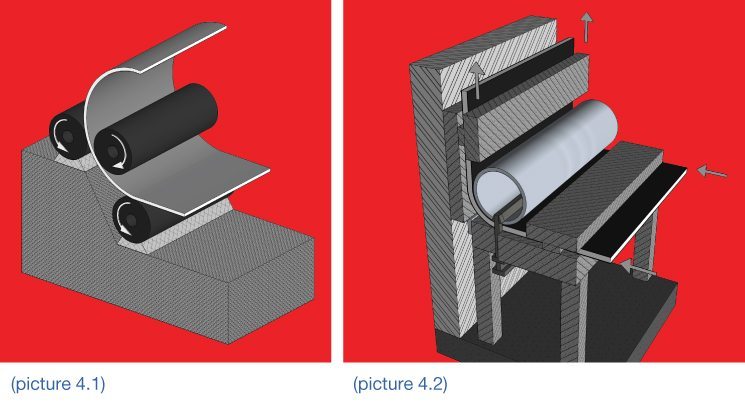
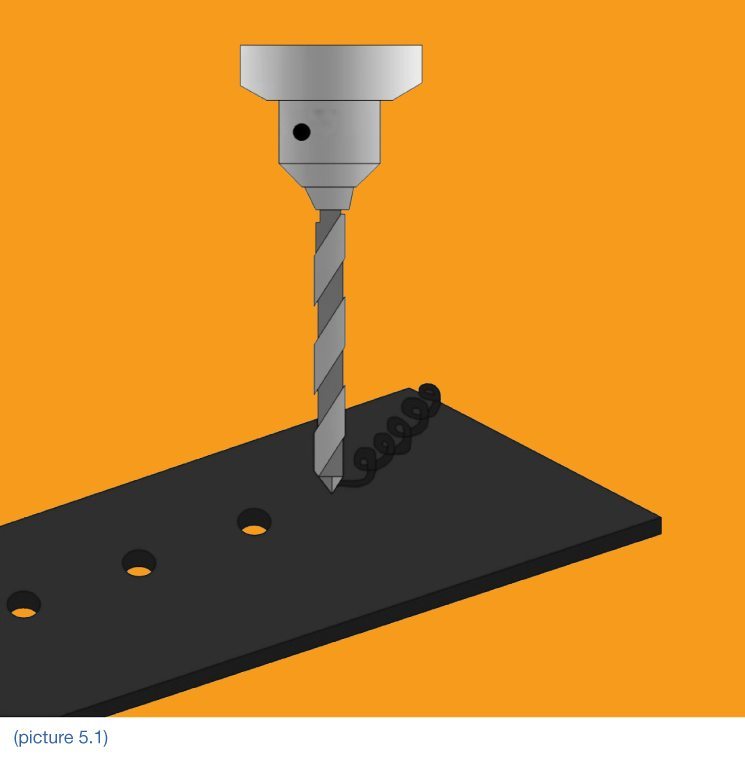
04 DRILLING
Alcotuff can be drilled using drilling tool for plastic or aluminum (see pict 5.1)
04 DRILLING
Alcotuff can be drilled using drilling tool for plastic or aluminum (see pict 5.1)
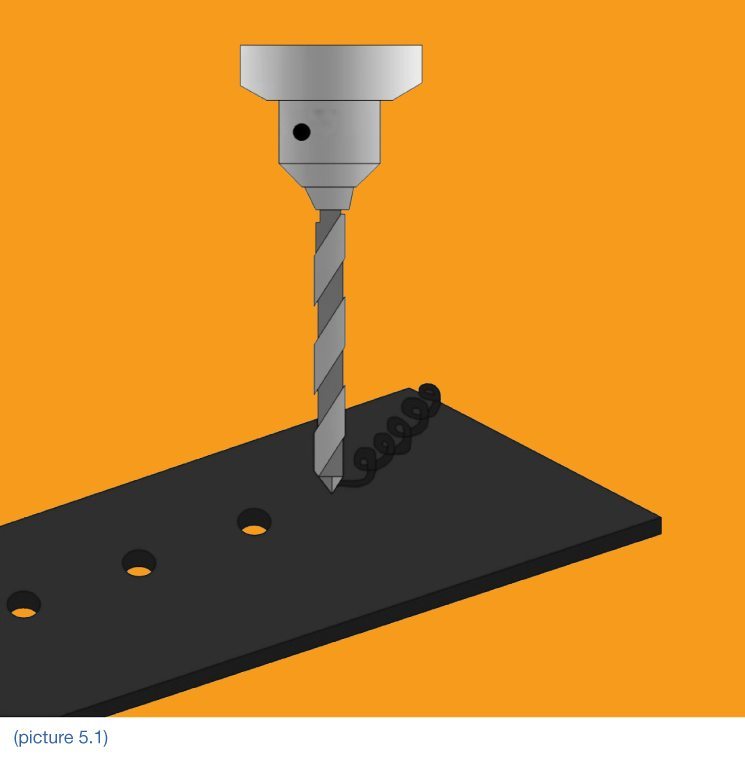
05 PUNCHING
A punching press can be used for notching and cutting out. The suitable clearance between punch and die is 0.1mm.(see pic 6.1)
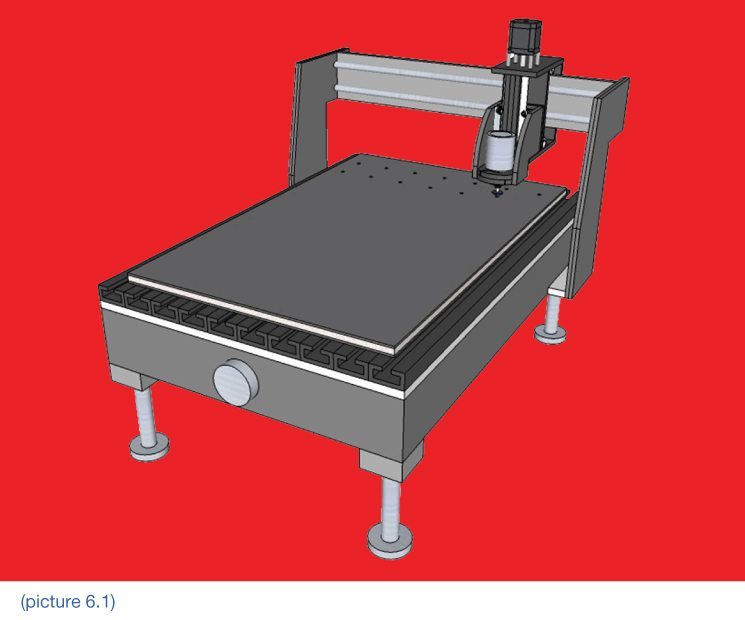
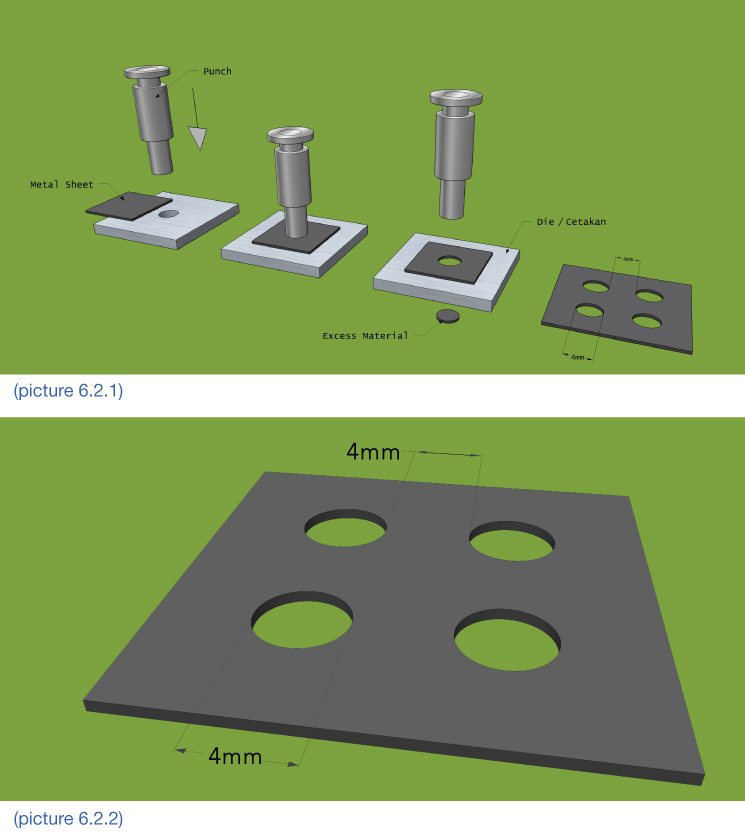
06 PERFORATING
For interior and ceiling design, Alcotuff can be perforated using CNC puncher (see pic 6.1). The minimum diameter of a hole can be punched is 4mm, and the minimum distance between holes is also 4mm. (see pic 6.2.1 – 6.2.2)
The best result is achieved using a single punch, multi punch is more economical, but further flatness processing is required to ensure the uniformity of the surface is regained.
06 PERFORATING
For interior and ceiling design, Alcotuff can be perforated using CNC puncher (see pic 6.1). The minimum diameter of a hole can be punched is 4mm, and the minimum distance between holes is also 4mm. (see pic 6.2.1 – 6.2.2)
The best result is achieved using a single punch, multi punch is more economical, but further flatness processing is required to ensure the uniformity of the surface is regained.
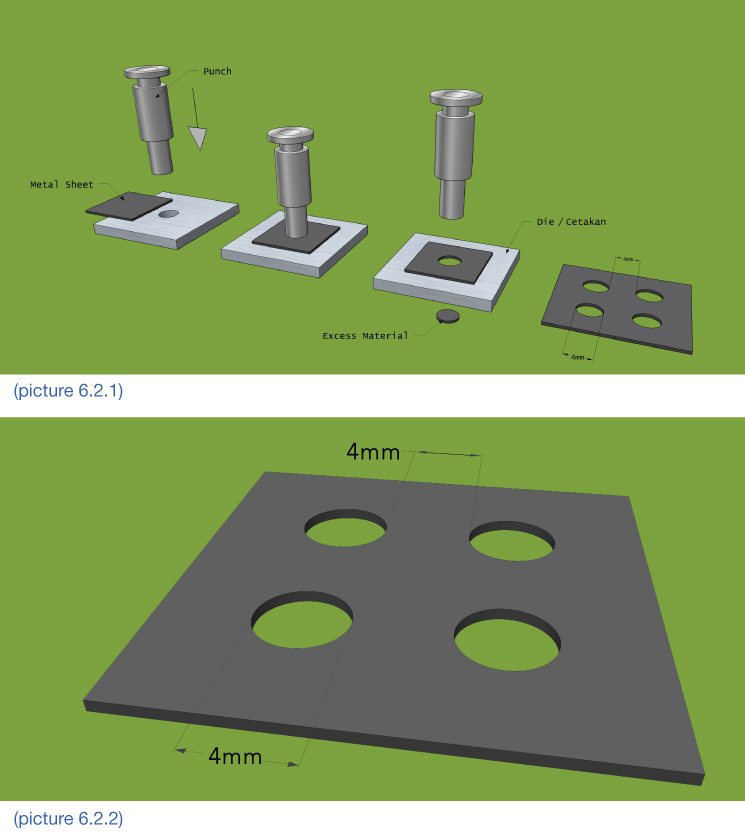
INSTALLATION
This is the basic information on the installation of ACP. Please read and follow the installation’s instruction carefully before starting. For more detail information, please refer to ACP manual installation book.
01 MASKING
Install Alcotuff in the same direction with the arrows printed on the masking. This is to avoid possible reflection differences among the installed sheets.
Only take off Alcotuff masking film after the installation is completed, taking off the masking during the installation might damage or scratch Alcotuff.
Remove the masking before 45 days, after that, it might be difficult to be removed.
Ensure to use the hand gloves while removing the masking film to ensure no finger print on Alcotuff surface.
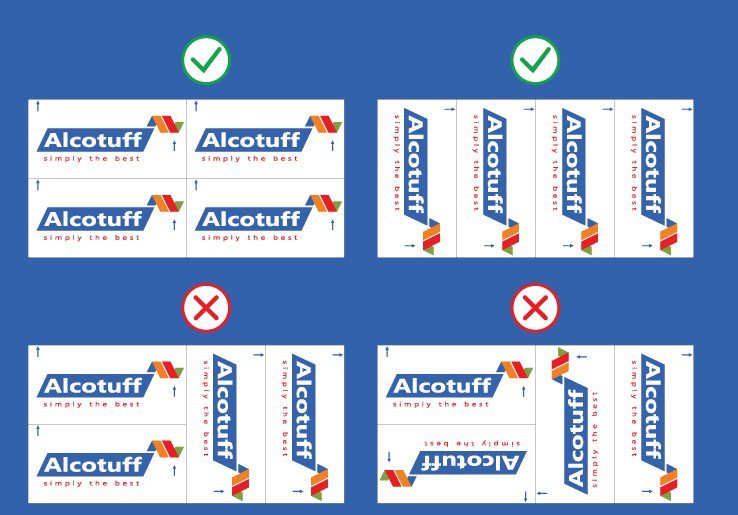
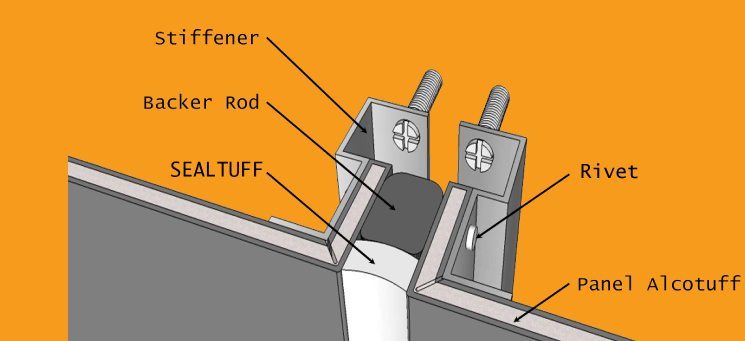
02 JOINT SEALANT
Low to medium modulus sealant is recommended to close the gap between panels to ensure expected joint width movement capability is achieved.
The sealant applied over a foam back rod, the depth of the sealant is recommended half time of the width gap.
For the best joining result, use Sealtuff, the high performance hybrid sealant.
02 JOINT SEALANT
Low to medium modulus sealant is recommended to close the gap between panels to ensure expected joint width movement capability is achieved.
The sealant applied over a foam back rod, the depth of the sealant is recommended half time of the width gap.
For the best joining result, use Sealtuff, the high performance hybrid sealant.
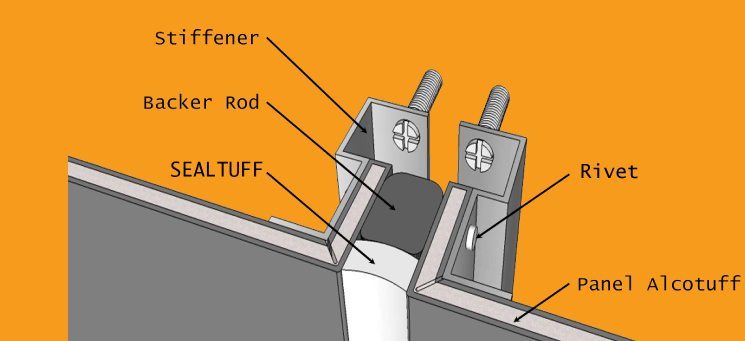
CLEANING AND MAINTENANCE
regular cleaning and maintenance is necessary to preserve the color and ensure the durability of Alcotuff. At least an annual Inspection and cleaning is recommended, depending on the surrounding environment.
Alcotuff can be cleaned using a soft sponge or a high-pressure water (max 50 bar). If needed, max 10% mild cleaning agent at Ph 6-7 can be mixed in the water. A trial on a smaller surface is recommended to ensure that this liquid mixture doesn’t affect Alcotuff surface.
Surface heated by the sun over 40 °C is not recommended for the cleaning process as the quick drying might cause blemishes all over the surface. Wait till the temperature goes down.
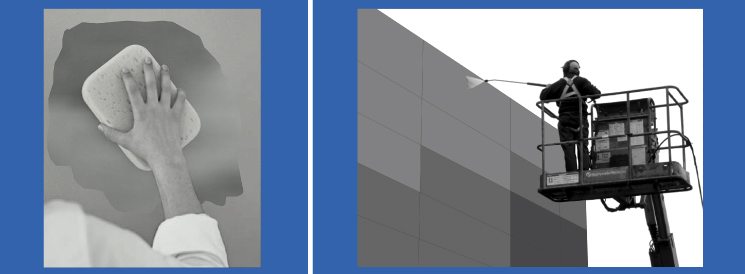
STORAGE
Please keep Alcotuff in a dry place and away from the sun. Exposure to direct sunlight for long time might cause the difficulty to remove the masking film.
Ensure the temperature stability of the storage place to avoid any condensation that might damage the surface of the sheet.
Store Alcotuff horizontally to avoid bending on the panel surface. When piling the sheet on a pallet, ensure to heap only sheets with the same sizes. It is also not recommended to stack the pallet one over the other.
ALCOTUFF
A PREMIUM ALUMINIUM COMPOSITE PANEL FOR PREMIUM BUILDINGS
Get complete information about the specifications and features of Alcotuff.
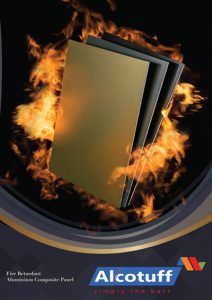